Introduction:
Copper Rotor
“Copper Rotor” is the rotor for squirrel cage induction motors which made from copper or copper alloy. Pressed by die casting machine under high pressure and velocity, the molten copper was injected into the mold and combined with silicon steel lamination injected to form the rotor.
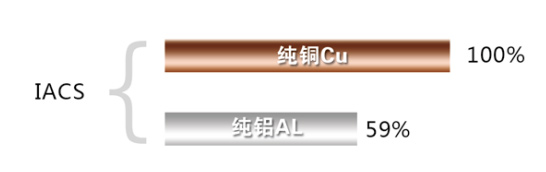
The motor performance could be improved a lot by using copper rotor technology.
Higher efficiency
The electrical conductivity of rotor could be decreased by 40% by using copper rotor to replace aluminum rotor. That could decreased rotor losses effectively and increased motor efficiency subsequently. The smaller of the motor, the higher percentage of the rotor losses accounted for the total motor losses, and the more efficiency improvement by using copper rotors.
Higher reliability
Due to the decreasing of motor loss, less energy converted into heat, which means the decreasing of working temperature of rotor as well as stator. Lower working temperature of means higher reliability and longer working life. Meanwhile, lower working temperature make it possible to use smaller cooling fans, which could decreasing of the mechanical loss, vibration and noise.
Higher energy density
Copper rotor technology could increase the motor energy density, which makes it possible to decrease motor frame size by 1 - 2 grades under the same output power, and reduce the motor weight by 20 % the same time.
Flexible design
Copper rotor technology makes it possible to develop 2 series products for different efficiency level(For example, IE4 — copper rotor, IE3- aluminum rotor ) under 1 series of stators. Meanwhile, motors could cover even wider output power range under limited frame size by using copper rotor technology.
Anti-corrosion
Copper has excellent corrosion resistance, it could work well under most of corrosion condition. Copper rotor is suitable for corrosion applications such as navigation, sea farming, chemical pump, etc.
The company product introduction
Brass rotor
Brass rotor is suitable for lifting application where higher starting torque and reliability are needed.
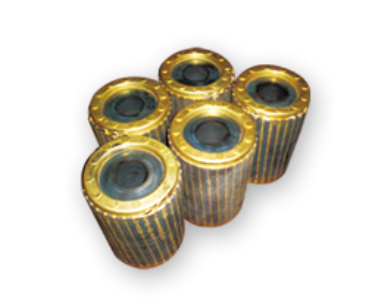
Copper and copper alloy foundry goods
YCD is capable to produce pure copper as well as copper alloy casting products.
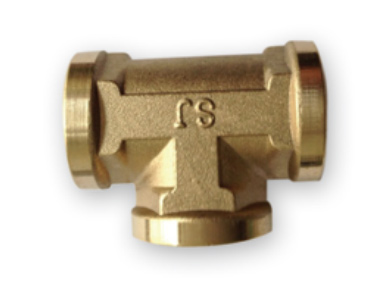
Super efficiency copper rotor motors
YCD could provide IE4 copper rotor motors as well as IE5 copper rotor motors.
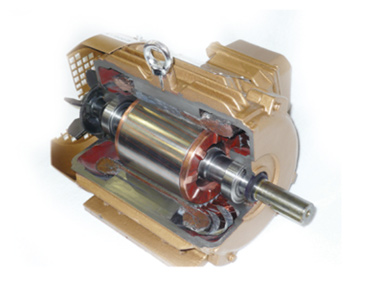
YZTE4
KW | 2P | 4P | 6P |
0.75 | 80M | 80M | 90S |
1.1 | 80M | 90S | 90L |
2.2
| 90L | 100L | 122M |
3 | 100L | 100L | 132L |
4 | 112M | 112M | 132M |
5.5 | 132S | 132S | 132M |
7.5 | 132S | 132S | 160M |
11 | 160M | 160M | 160L |
15 | 160M | 160L | 180L |
18.5 | 160L | 180M | 200L |
22 | 180M | 180L | 200L |
30 | 200L | 200L | 22SM |
37
| 200L | 22SS | - |
45 | 22SM | 22SM | - |
Application of copper rotor
Industrial high efficiency motors.
The demand of high efficiency motor is increasing along with the improvement of the minimum motor efficiency standard. Copper rotor technology is the most economical and easy way to make motors meet the requirement of higher efficiency. In China, copper rotor technology was listed into the National Promotional Catalog of Key Energy Saving Technology, meanwhile, the 12th 5 Years Plan of Energy Saving and Environment Protection published by the State Council also list Copper rotor technology as the solution to high efficiency motors.
Motor Rebuilt
Copper rotor could be used to refurnish the current used old motors to improve the installed motor efficiency. It could improve the old motor efficiency by 1-2 grades by used the new designed copper rotor to replace the aluminum rotor. That gives an easy and economical way to change the old, need be eliminated motor to high efficiency motor which totally meet the requirement of the energy efficiency standard.
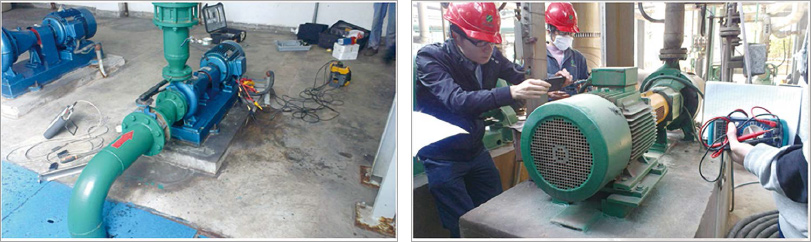
Improving energy density
The physical size and weight of motor could be decreased by using copper rotor technology. For example, 75KW-2 motor for compressor, the motor frame size is 280 by using aluminum rotor, if use copper rotor technology, the frame size could be decreased from 280 to 225, meanwhile, the efficiency could be improved from IE2 to IE3. Copper rotor technology makes it possible to improve motor efficiency together with reduce physical size, and reduce cost subsequently.
Copper rotor technology gives more flexibility to motor manufacturers. By using copper rotor or aluminum rotor, motor manufacturers could produce 2 different efficiency motor under the same stators. That makes it possible to develop 2 series product of different efficiency under 1 series stator. Meanwhile, motors could cover even wider output power range under limited frame size by using copper rotor technology.
Electrical Vehicles
The induction motor solution with copper rotor technology is one of the best solutions for driven motor for electrical vehicles. The most successful electrical vehicles currently in the world, has adopted copper rotors for their driven system. Copper rotor motor has higher efficiency, mature control system. higher reliability, lower cost when compared with other solutions.
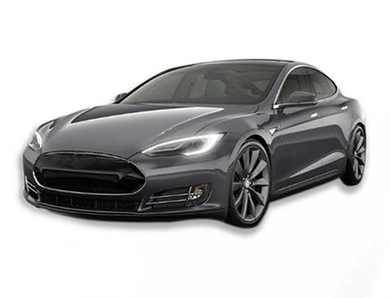
Other application
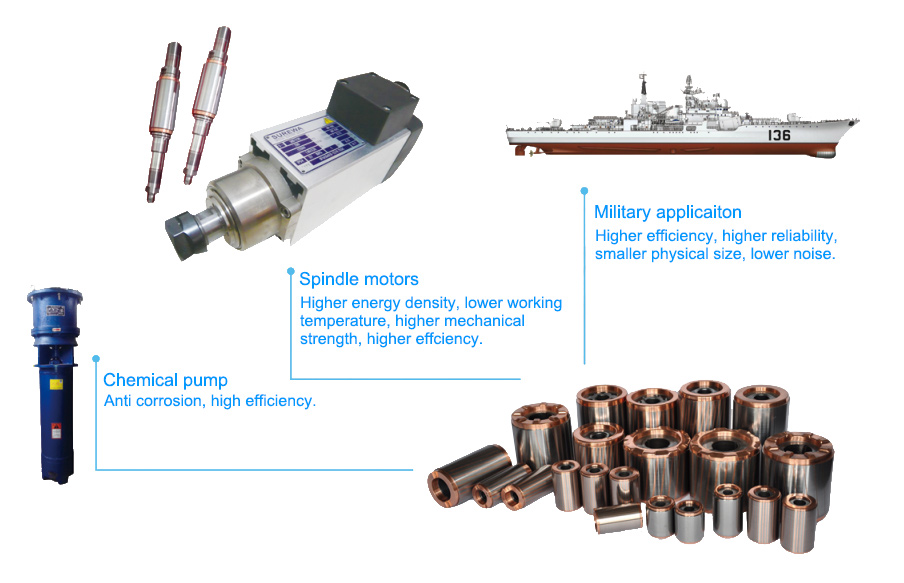
Competitive advantage of YCD
Material
The YCD’s copper rotor used high quality cathode copper produced by Yunnan Copper Group. The purity exceeded 99.95%. All runners, biscuits and oddments were collected to the refining process in Yunnan Copper Group, which make sure every copper rotor was produced by new high quality pure copper to ensure the high performance of rotor.

Equipment
The YCD’s press machines were imported from the Switzerland, which has the excellent performance and real-time control system. These equipments ensured the consistence of the production process and the high quality of produce subsequently.
The advanced equipments with original technology make YCD capable to produce high quality copper rotors and other copper & copper alloy die castings.

Technology
Yunnan Copper Group began to develop copper rotor technology from 2004. Based on more than 10 years effort, YCD has developed a whole solution to produce copper rotor commercially which including the production process, tooling technology, smelting process, casting process, product inspection, etc. YCD has owned 8 patents including 3 patents of invent.
As the member of International Copper Association (ICA), YCD got a Jot technical support from ICA, which helps YCD to produce copper rotor with global leading quality. Yunnan Copper Group, which is the mother company of YCD, has plenty of experience of copper Processing technology, YCD also got sufficient technical support from Yunnan Copper Group. YCD was honored as the creative studio of mechanical and metallurgical industry of China, academician workshop, creative studio of Yunnan Province.
Quality control
YCD has passed the IS09001 :2008 and fully control the whole process including product design, production and inspection by using PFMEA, standard processing guidance, SPSS, etc.
YCD has developed copper die casting simulation software by collaborated with Tsinghua University. The software can be used to simulate the temperature field and the casting process, which improved the tooling design capacity.
YCD has developed rotor quality inspection equipment, which could be used to test the quality and inner defects of rotors.
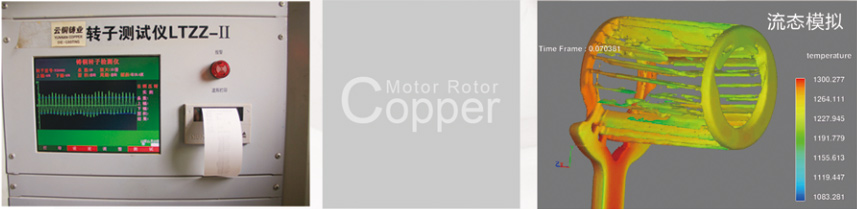
The necessity of increased motor efficiency
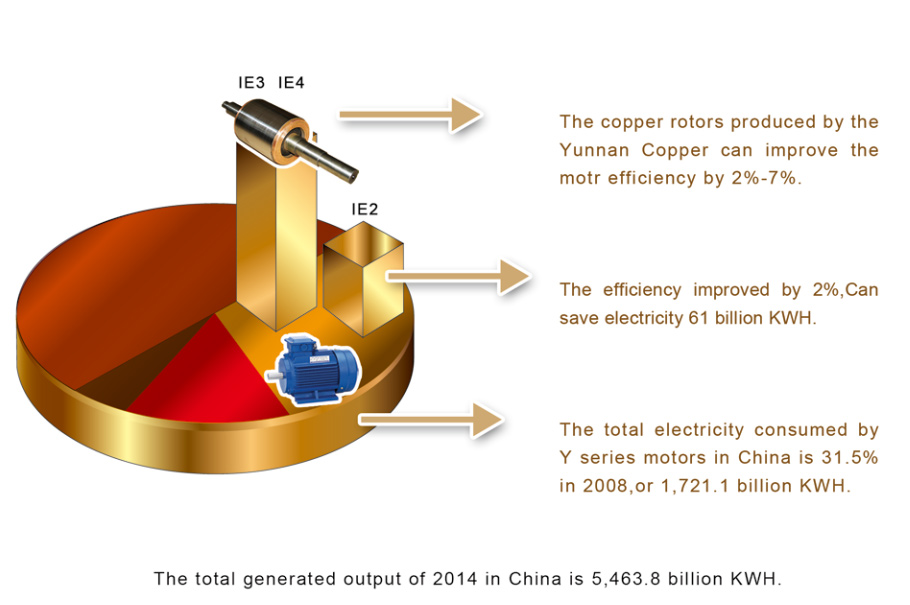
Middle-&small-sized asynchronous motors are the main power sources in Chinese industry. According to data from the NDRC, the Chinese generating capacity in 2014 was 5463.8billion KWH. 50% of that was consumed by motors, of which 90% was consumed by three phrase asynchronous motors. And Y series motors consume 70% of that amount. In other words, Y series motors consumed 31.5% of the Chinese power generating capacity (1721.1 billion KWH).
If all these motors were to be substituted for high efficiency motors (IE2 and IE3), nearly 61 billion KWH of electricity would be saved. This amount is equal to six months of the power generating capacity of the Three Gorges Hydropower Station, and would save about18.3 million tons of standard coal. This reduction in coal would reduce the emission of carbon dioxide about 47.93 million tons.
All the CMRs by YCD can increase efficiency of CRM from 2-7 percent in comparison to their aluminum equivalent, the energy-savings are remarkable. In real-life comparison between 5.5kw CRM and aluminum one to drive fan, the CRM saved 1837 KWH of electricity annually (running for 330 days). This savings equated to about 1249Yuan RMB. (0.68yuan/KWH)